Сварочная проволока 3 мм ГОСТ 2246-70
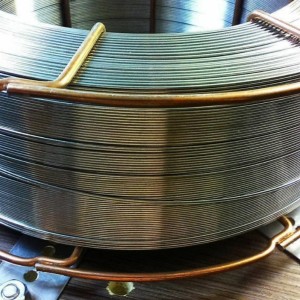
- ГОСТ/ТУГОСТ 2246-70
- Диаметр, мм3
- ГОСТ/ТУГОСТ 2246-70
- Диаметр, мм3
Описание Сварочная проволока 3 мм ГОСТ 2246-70
Сварочная проволока 3 мм ГОСТ 2246-70 в наличии на складе в Стерлитамаке от компании «Инметпром». Закажите сварочная проволока 3 мм ГОСТ 2246-70 по номеру телефона +7 (347) 299-64-67, отправив запрос на электронную почту sterlitamak@inmetprom.ru или заполнив форму обратной связи на нашем сайте.
Наши специалисты ответят на все вопросы, касающиеся наличия товара, вариантов оплаты и сроков доставки.
Оставить отзыв или задать вопрос
Как оплатить заказ?
Оплата товаров производится при помощи любого удобного для вас способа:
- наличными или безналичными средствами через расчетный счет, а также по факту получения товара.
Подробнее с ними можно ознакомиться на соответствующей странице.
Доставка
Вы можете выбрать любой подходящий для вас вариант с нашим специалистом по логистике:
- до склада, самовывозом, «до дверей».
Он поможет подобрать оптимальный маршрут и транспорт, а также сориентирует вас о примерных сроках и стоимости доставки. Цифры могут отличаться в зависимости от сезона!
Проволока СВ-06Х19Н9Т (стабилизированная титаном) обеспечивает высокую устойчивость сварного шва к межкристаллитной коррозии (МКК) после сварки нержавеющей стали 08Х18Н10Т без последующей стабилизирующей термообработки. Это подтверждается стандартными испытаниями по методу АМУ ГОСТ 6032-2017. Присутствие титана в проволоке связывает углерод в карбиды титана, предотвращая обеднение границ зерен хромом.
Тонкое медное покрытие на сварочной проволоке СВ-08Г2С-О (толщина обычно до 0.3 мкм) предназначено в первую очередь для улучшения токоподвода и защиты самой проволоки от атмосферной коррозии при хранении и транспортировке. На коррозионную стойкость выполненного сварного шва в пресной речной воде (pH ~7.2) это покрытие практически не влияет; стойкость шва определяется его собственным химическим составом (близким к СВ-08Г2С).
На сварном шве из проволоки СВ-08Г2С (углеродистая сталь) при хранении сварного изделия на открытом воздухе в прибрежной зоне (содержание хлорид-ионов в атмосфере ~0.5 мг/м³) видимый слой ржавчины (покрывающий более 10% поверхности) образуется очень быстро, вероятно, в течение нескольких недель, максимум 1-2 месяцев, при отсутствии защитного покрытия. Через 6 месяцев степень коррозии будет значительной.
Использование сварочной проволоки для алюминия марки СВ-АК5 (содержащей 5-6% кремния) для изготовления элементов бижутерии, которые будут непосредственно контактировать с кожей человека, не рекомендуется. Хотя сам алюминий и кремний считаются относительно инертными материалами, возможны индивидуальные аллергические реакции на компоненты сплава или продукты его окисления. Кроме того, внешний вид такого изделия со временем может изменяться.
Недостаток применения активированной сварочной проволоки (например, СВ-08Г2С-А, содержащей повышенное количество раскисляющих и микролегирующих элементов) для сварки сталей с высоким содержанием углерода (более 0.45% С) может заключаться в увеличении склонности металла сварного шва к образованию горячих (кристаллизационных) трещин. Это связано с влиянием активирующих добавок на процесс кристаллизации металла шва и расширение температурного интервала хрупкости.
Для высокопроизводительной роботизированной сварки длинномерных швов однозначно предпочтительнее использовать сварочную проволоку, поставляемую на катушках или в упаковках большого веса (например, 250 кг в специальных картонных бочках типа "марафон" или на большегрузных металлических катушках). Это позволяет минимизировать частоту остановок робота для замены катушек, тем самым значительно повышая коэффициент использования дорогостоящего оборудования и общую производительность сварочного процесса.
Для сварки высокопрочной стали S690QL (с пределом текучести 690 МПа) требуется применение сварочной проволоки, обеспечивающей равнопрочность сварного соединения, например, марок СВ-10ХГ2СМФ или СВ-08ХН2ГМТЮ. Эти проволоки легированы комплексом элементов (Cr, Mn, Si, Mo, V, Ni, Ti), которые обеспечивают получение необходимых механических свойств и высокую стойкость к образованию трещин. Конкретный выбор зависит от условий эксплуатации и требований к ударной вязкости.